Lean Business Technology
Continued from Friday
Components are integrated over an enterprise service bus that
supports the assembly and re-configuration of applications that
ultimately enable the common capabilities of the business. Legacy
systems are initially wrapped so that they can be integrated over the
service bus, and eventually rationalized out in a cycle of continuous
improvement and waste reduction.
Business benefits can be substantial. By reducing redundancy and
complexity, platforming reduces the cost of maintaining systems and
integrating new components. As the core processes of the business are
incrementally improved, the underlying application components are able
to keep pace. Components are smaller; integration is standards based.
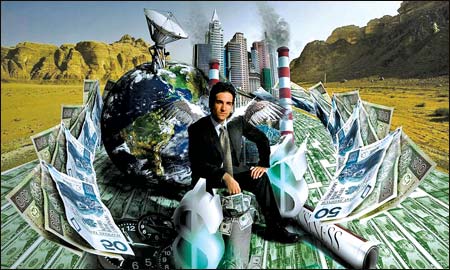
The enterprise is more agile and resilient to change; it becomes
“Lean”. 3. Lean Methods Lean Business Technology is based on a
service-oriented paradigm; it is also a fundamentally different way of
working.
It is a better way to drive collaboration between business and IT to
deliver improved business performance. Toyota was able to become the
world’s leading car company not through the theory of just-in-time, or
statistical quality control - but through the Toyota Way.
Often business change programmes are launched with great fanfare and
burning platforms. The Toyota Way makes business change and improvement
part of the daily work of everyone at Toyota. Customers work with
marketing people who work with engineering people who work with factory
workers on the floor.
Quality is improved by promoting a culture of quality in the small
teams who work daily with their specific components. The team is the
source of seemingly small and incremental improvements that have added
up to a core process that consistently delivers the highest quality
products in the world.
An Agile-based approach to systems development works well within LBT.
Large, complex programs are delivered incrementally. Programs are
organised into smaller, self-directed teams of business and IT people
that deliver new or improved services in sprints.
These smaller teams are focused on providing the right quality of
service that their common capability will deliver. Software components
are designed and assembled out of the platforms to provide the
applications required. Each component being developed is thoroughly
tested in an environment that predicts the end customer’s experience of
the service being delivered.
In Lean methods, the quality of service delivered by a component is
the primary focus. Getting something wrong always degrades a customer’s
experience - the challenge is getting it right first time every time.
Lean methods represent the desired customer experience through
“customer stories” that describe a customer’s journey through a specific
narrative of a core process. These stories are decomposed into the
common capabilities and components that together deliver the services
into this end-to-end customer experience.
Conclusion The 2009 JD Power customer satisfaction survey ranks
Toyota’s Lexus as the “most satisfying brand” for the ninth year
running. In this latest survey, the Lexus RX takes first place in the
individual car category.
The Toyota Prius claims second. While the current economic conditions
are difficult for their industry, and other companies are going
bankrupt, Toyota will clearly weather the storm. From modest beginnings,
Toyota is now larger than Ford and GM combined, with a net margin that
is over three times the auto industry average.
At the heart of Toyota is a Lean Manufacturing method that drives
daily continuous improvement within the company. Now the Toyota Way has
gone beyond the mass production of automobiles and is a heartbeat for
all other types of manufacturing. The revolution is now starting in the
service industries to apply lean thinking to improve quality and drive
out waste.
LBT is a new way to apply lean methods to business process
improvement and IT. LBT offers a way for IT to apply the proven
approaches of leading companies like Toyota to lower costs, reduce cycle
time, and deliver the highest quality experience to its customers. |